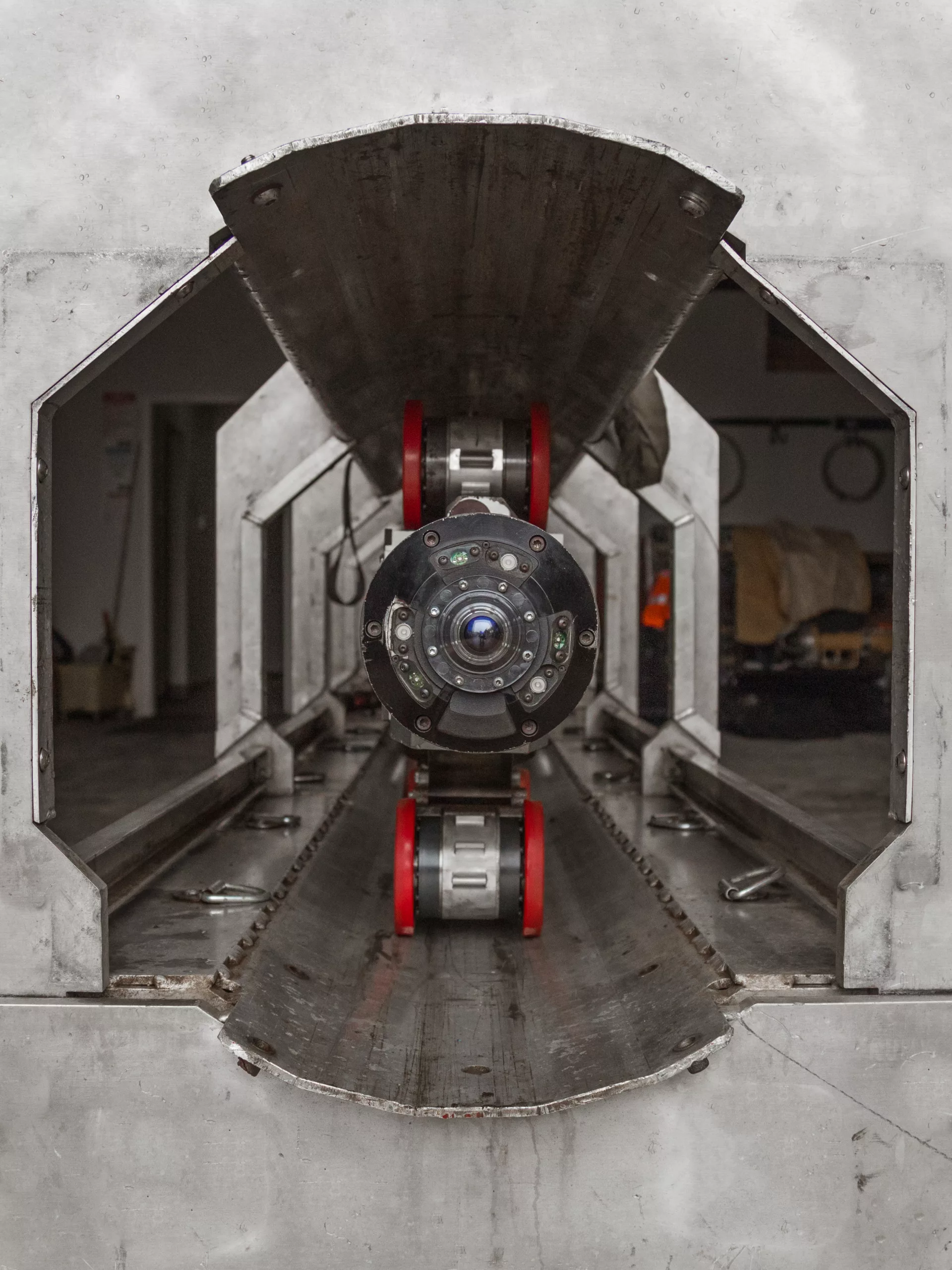
Ensuring Pipeline Safety with Advanced Robotic Inspection
In early 2022, we introduced a revolutionary sensor technology designed to address the integrity concerns associated with long seam welds in pipelines that are challenging to inspect. Through extensive research, development, and testing, Intero successfully integrated a circumferential magnetic flux leakage (CMFL) sensor into its Pipe Explorer robotic pipeline inspection platform. This innovation, supported by NYSEARCH and the Northeast Gas Association, represents a significant advancement in pipeline inspection technology.
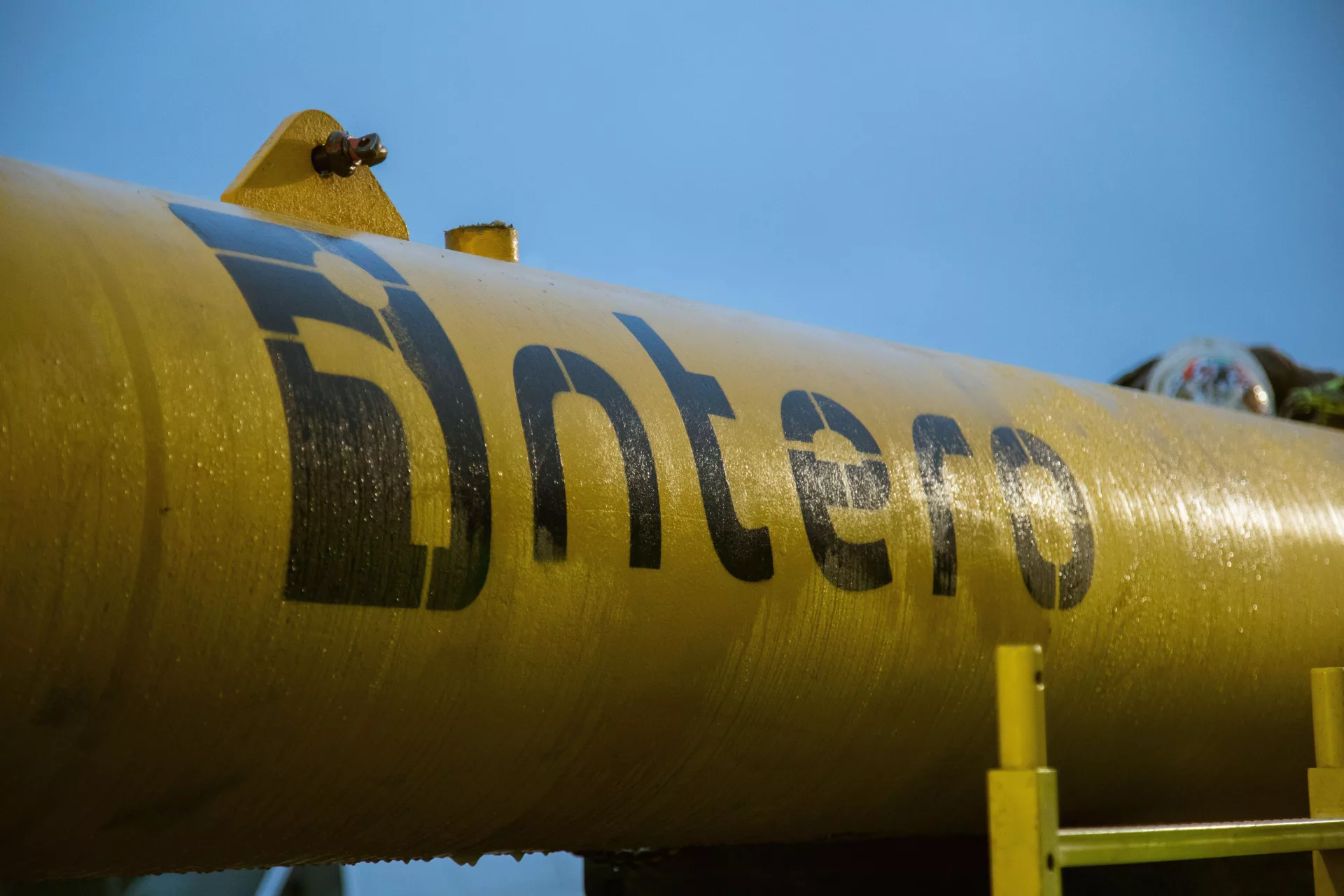
The Challenge of Long Seam Welds
Long seam welds in pipelines, particularly those made from low-frequency-welded ERW and flash-welded pipes, are prone to various integrity issues. These include selective seam weld corrosion, cracks, and other anomalies that can lead to significant environmental hazards if not properly managed. Traditional free-swimming inline inspection tools are often incompatible with these pipelines due to physical barriers, lack of necessary infrastructure, or unsuitable operational conditions, rendering these pipelines unpiggable.
Intero’s Innovative Pipeline Inspection Solution
Intero's Pipe Explorer robotic inspection system addresses these challenges by offering a reliable alternative for inspecting difficult-to-inspect pipelines. Unlike free-swimming tools, which rely on pipeline pressure for propulsion and lack control, the Pipe Explorer uses internal motors and can be maneuvered in real-time. This allows for precise navigation and comprehensive data collection, even in pipelines with complex configurations.
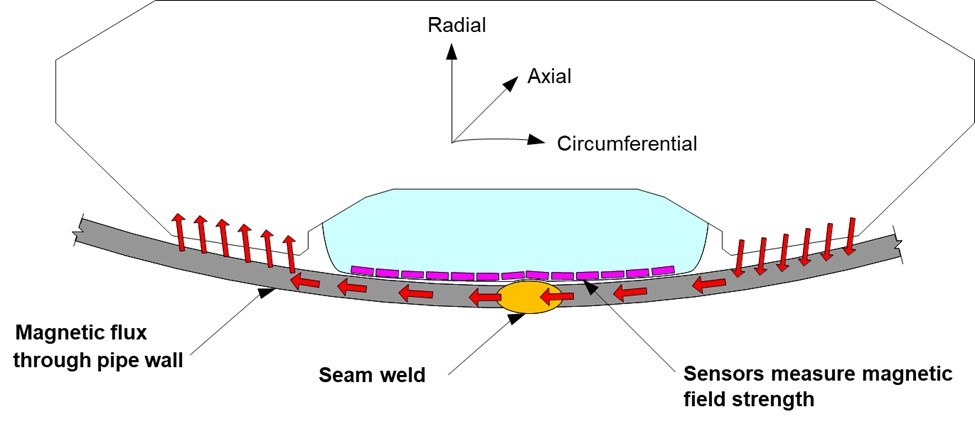
CMFL Sensor Technology
Real-Time Control
Comprehensive Data Collection
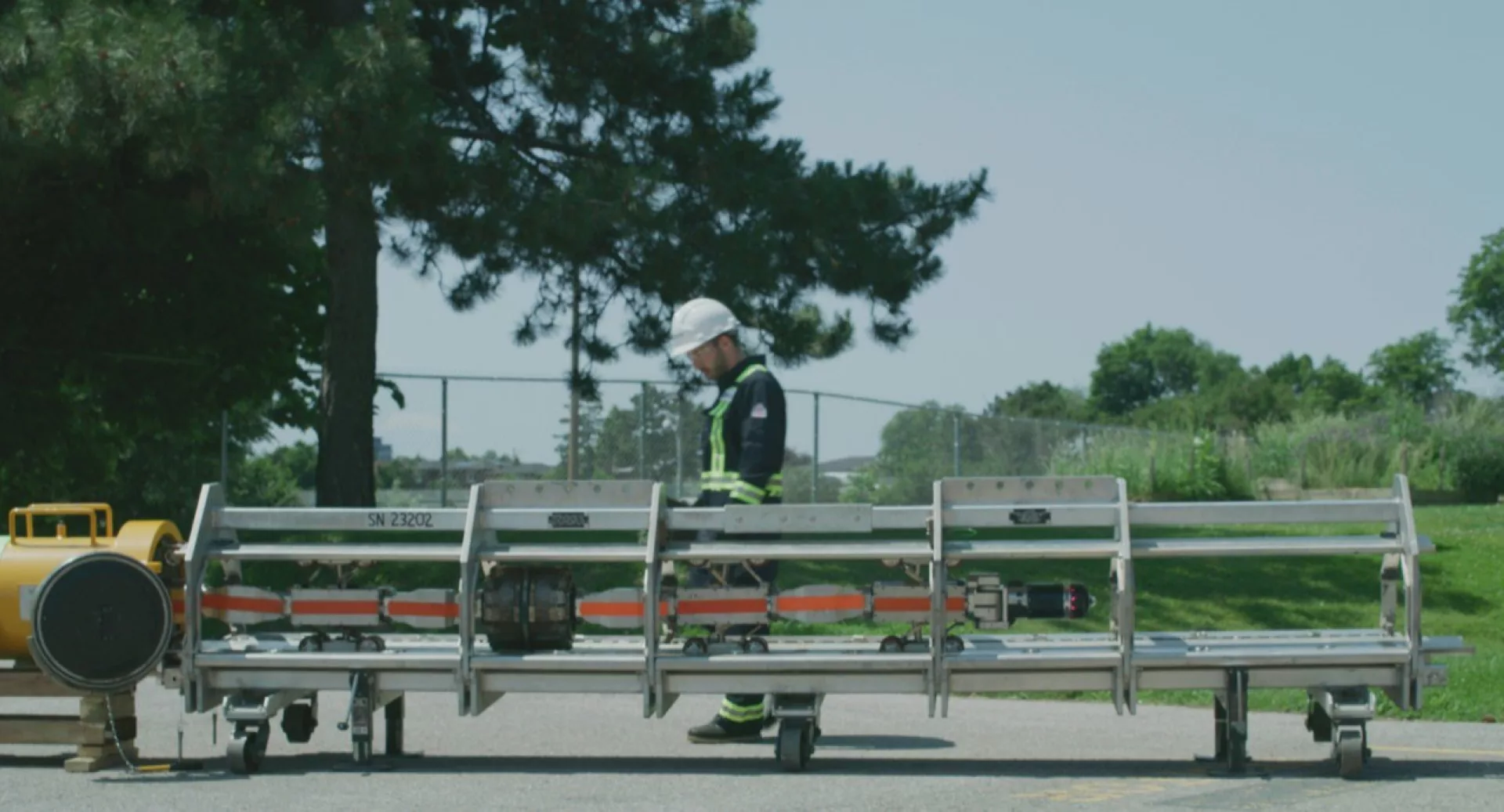
Proven Results in Pipeline Safety
Since its deployment, we has assessed over 30 kilometers of pipelines using the robotic inspection method, significantly improving the safety and integrity of these infrastructures. The data collected has been instrumental in facilitating proactive maintenance efforts and addressing various issues, such as selective seam weld corrosion.